jan 22, 2019 | Processo de soldagem
A soldagem é um processo que requer muita habilidade, conhecimento dos materiais e dos procedimentos por parte do soldador. Por isso é sempre importante que exista a necessidade da qualificação dos processos de soldagem e dos soldadores envolvidos, tendo nas normas de soldagem ASME IX uma das mais importantes.
Considerado como um código que estabelece todos os requisitos de qualificação de procedimentos de soldagem e brasagem, a norma de soldagem ASME IX é de extrema importância para o setor, pois estabelece critérios básicos para a os processos de soldagem.
Assim, para executar a soldagem com segurança e eficiência, inúmeros critérios são consolidados e previamente validados por uma série de testes/ensaios para cada situação de soldagem, que se fazem presentes na ASME IX.
Veja neste conteúdo algumas informações sobre essa norma para que o procedimento de soldagem seja o melhor possível.
![[Infográfico] Conheça os EPIs obrigatórios para processos de soldagem [Infográfico] Conheça os EPIs obrigatórios para processos de soldagem](https://www.treal.com.br/blog/wp-content/uploads/2018/09/Display-Infográfico-EPI-1024x237.jpg)
Normas de soldagem ASME IX: Você sabe o que são?
ASME é uma sigla em inglês que significa: “The American Society of Mechanical Engineers” (Sociedade Americana de Engenheiros Mecânicos).
A ASME representa um conjunto de normas e na sua seção 9, conhecida como ASME IX, há a determinação de parâmetros para qualificação de soldadores e procedimentos de soldagem, principalmente em virtude do grande número de variáveis envolvidas nos processos de soldagem.
Todas essas variáveis precisam ser validadas por uma série de testes/ensaios destinados a cada situação de soldagem, recebendo assim a qualificação.
As normas de soldagem ASME IX determinam que cada soldador qualificado deve possuir uma espécie de código que funciona como uma ”carteira de identidade”. Dessa forma um soldador que tem o código relacionas às normas de soldagem ASME IX é um profissional testado e capacitado para atender aos requisitos de soldagem.
Documentos de validação dos processos de soldagem
Todas as validações relacionadas às Normas de soldagem ASME IX são inseridas em documentos conhecidos como:
- Especificação de Procedimento de Soldagem (EPS);
- Registro de Qualificação de Procedimento de Soldagem (RQPS);
- Registro de Qualificação de Soldador (RQS).
Esses documentos englobam todos os critérios e limites relacionados à atividade de soldagem. Veja mais sobre esses documentos a seguir.
Especificação de Procedimento de Soldagem (EPS)
Também chamado de Especificação de Soldagem ou Procedimento de Soldagem da Executante, o EPS é um procedimento de soldagem escrito e qualificado que é emitido pelo fabricante com o objetivo de fornecer informações relacionadas à técnica de soldagem a ser utilizada e que devem atender aos requisitos do código de qualificação.
Basicamente, este documento descreve como uma solda deve ser realizada na produção, por isso deve conter todas as variáveis essenciais e variáveis essenciais suplementares (quando requerido) para cada processo de soldagem utilizado, indicando também parâmetros aceitáveis para diversas variáveis do processo.
Na soldagem, variáveis do procedimento que podem fazer parte de uma EPS incluem:
- Composição química;
- Classe e espessura do(s) metal(is) base;
- Processo(s) de soldagem;
- Tipos de consumíveis e suas características;
- Projeto da junta;
- Posição de soldagem;
- Temperatura de pré-aquecimento e entre passes;
- Corrente, tensão e velocidade de soldagem;
- Aporte térmico;
- Número aproximado de passes;
- Características do tratamento térmico após a soldagem (quando este é usado).
Informações complementares que o fabricante julgar úteis ou necessárias para gerar uma melhor qualidade da solda podem também ser colocadas neste documento.
Registro de Qualificação de Procedimento de Soldagem (RQPS)
Este documento representa o registro dos dados utilizados para soldar um corpo de prova (chapa ou tubo de teste).
Neste documento devem ser anotados os valores reais das variáveis essenciais, além de, quando requerido, variáveis essenciais suplementares efetivamente utilizadas no processo de soldagem da chapa ou tubo de teste. Deve também conter os resultados dos testes executados para a qualificação do procedimento.
Dentre as diversas recomendações, o RQPS deve indicar o tipo de junta que foi soldada ou as dimensões da chapa de teste. Já a sequência de soldagem deve constar no RQPS no croqui da junta.
Registro de Qualificação de Soldador (RQS)
Por fim temos o RQS. Este documento atesta a habilidade do soldador em executar os variados tipos de soldas de acordo com EPS qualificadas e as normas de soldagem ASME IX.
Sobre o documento de RQS são anotadas as variáveis essenciais utilizadas pelo soldador na execução de uma chapa ou tubo de teste, bem como suas faixas de qualificação e os resultados dos testes executados.
Por que ter qualificação ASME IX?
Como já dito, os processos de soldagem necessitam de muita habilidade e conhecimento por parte dos soldadores. Dessa forma, as normas de soldagem ASME representam uma forma de garantir qualificação que estabelecem critérios básicos para a soldagem, os quais devem ser observados na preparação dos requisitos de soldagem.
Assim, tanto o Procedimento de Soldagem (EPS) quanto o Registro de Qualificação do Procedimento (RQP) objetivam determinar que a soldagem proposta será capaz de atender as propriedades requeridas para a sua pretendida aplicação.
Mas, para isso, é importante, que o usuário (caso do soldador) compreenda e considere esses critérios básicos quando da Qualificação do Procedimento de soldagem.
Quer saber mais sobre os processos de soldagem? Então veja porque é tão importante investir em bons equipamentos de soldagem
jan 1, 2019 | Informativos, Processo de soldagem
O procedimento de corte de chapas de aço vem sendo cada vez mais utilizado em diversas indústrias, que requerem tais chapas para uso em setores de construção de maquinários e obras navais/civis e para a elaboração de ferramentas ou mesmo para aprimorar segmentos metalúrgicos ou hidráulicos.
Esse processo deve apresentar cortes de chapas de aço de boa qualidade, mas ao mesmo tempo deve atingir produtividade para que o processo de corte tenha maior eficiência e rendimento.
Dessa forma, para atingir significativos avanços quanto à produtividade do corte de chapas de aço é fundamental adotar algumas medidas. Quer conhece-las? Então acompanhe o nosso conteúdo a seguir.
Aspectos a considerar para aumentar a produtividade do corte de chapas de aço
A busca pela maior produtividade é recorrente em todos os processos dentro de uma indústria e é claro que com o corte de chapas de aço não pode ser diferente.
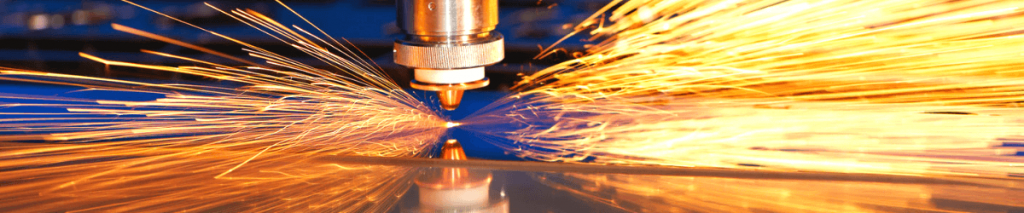
Dessa forma, trabalhar com maquinários de corte apropriados e desenvolvidos em conformidade com a maior produtividade é fundamental. Neste contexto, é muito importante considerar:
- Tipo de máquina utilizada;
- Sistema de corte ideal para cada espessura da chapa de aço;
- Dispositivo de controle de movimento da peça e, do maçarico (por exemplo, capacidade da máquina CNC e controle de altura da tocha);
- Variáveis inerentes ao processo (como a velocidade e altura de corte, escolha de consumíveis, entre outras variáveis);
- Variáveis externas (como por exemplo a variabilidade do material, pureza do gás, experiência do operador).
Neste sentido, se a indústria quer aumentar sua produtividade, é importante que ela considere todos esses fatores, melhorando a aparência do corte de chapas de aço e aumentando o nível de produção.
Dicas para aumentar a produtividade no corte a plasma
Comparado aos outros tipos de cortes (oxicorte e corte a laser) o corte de chapas de aço a plasma costuma oferecer velocidades de corte muito mais rápidas, elevando o nível de produtividade, por isso são bastante indicados.
Mas mesmo para o corte a plasma, alguns cuidados precisam ser demandados pela indústria. A seguir veremos alguns deles.
-
Realize o corte com uma maior amperagem (corrente)
Para alguns formatos de peças (os mais simples e sem contornos intrincados), é possível obter a mesma qualidade de corte com uma configuração de corrente mais alta, permitindo um corte mais rápido, ou seja, com maior produtividade, indicando ser possível aumentar a amperagem.
Alguns sistemas de plasma costumam oferecer uma ampla variedade de configurações de corrente para cada espessura, permitindo que se melhore tanto a qualidade como a velocidade do corte.
-
Mantenha os bicos de eletrodos sempre limpos
Manter a higiene na instalação de novos consumíveis impede possíveis falhas prematuras causadas por contaminação, tal fato irá contribuir com a maior produtividade.
Por isso, é importante que o estoque de consumíveis sempre esteja em um local seguro e as peças da tocha sejam guardadas em sua embalagem original até chegar o momento de usá-las.
Além disso, é recomendado que os consumíveis nunca acabem do estoque, impedindo que a máquina de corte de chapas de aço fique parada devido à falta de estoque destas peças críticas e essenciais.
-
Faça a manutenção constante da máquina de corte de chapas de aço
Qualquer problema na máquina de corte de chapas de aço pode significar a parada do processo por determinado período que consequentemente reduzirá a produtividade. Portanto, priorizar a manutenção da máquina de corte é fundamental para garantir seu uso continuo sem a “surpresa” da ocorrência de nenhum problema.
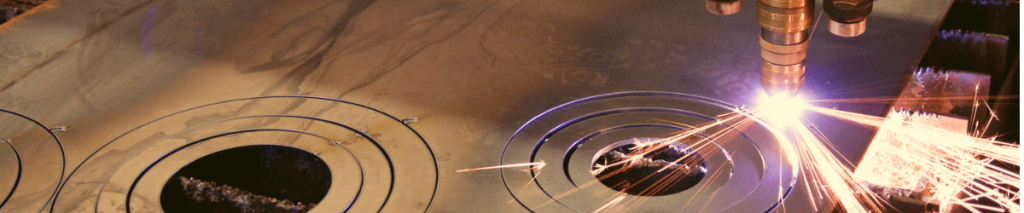
Além disso, manter a máquina limpa também ajuda na produtividade. Partículas do corte e fuligem que se acumulam nas máquinas precisam ser continuamente retiradas, reduzindo a contaminação das peças móveis e consequentemente resultando em menor desgaste.
-
Confira seu suprimento de gás
Nunca deixe faltar o suprimento de gás, caso contrário o processo irá parar no meio do caminho. Também é necessário fazer testes de vazamento regulares, certificando que o sistema de gás integral receba manutenção adequada.
-
Faça inspeções constantes durante todo o processo
Por fim, para que o processo de corte de chapas de aço seja o mais produtivo possível é importante que o processo seja monitorado constantemente. Esse monitoramento deve basear-se principalmente no trabalho do operador, sendo ele a “peça” mais importante desse processo em busca da produtividade.
Dessa forma, o monitoramento irá se basear nas seguintes perguntas:
- O processo escolhido é o ideal para a espessura a ser cortada?
- O arco plasma é cortado na direção apropriada?
- Os consumíveis estão gastos?
- A tocha está quadrada na peça de trabalho?
- A distância entre a tocha e o trabalho está ajustada na altura correta?
- A velocidade de corte de chapas de aço está correta?
- Há algum tipo de vibração na tocha?
As respostas a esses questionamentos e as respectivas ações corretivas de cada um desses aspectos serão fundamentais para garantir que a produtividade do corte de chapas de aço com o uso do plasma seja a melhor possível.
O soldador tem papel importante na busca pela produtividade. Mas para a sua segurança é importante conhecer os riscos pertinentes à profissão. Veja neste conteúdo os principais riscos!

dez 4, 2018 | Informativos, Processo de soldagem
Você tem uma oficina que realiza trabalhos de solda? Então você provavelmente busca o máximo de produtividade em seu processo de soldagem, certo? Mas você sabe como conseguir isso?
De fato, essa vem sendo uma necessidade comum a todos os soldadores, afinal, a produtividade significa produzir mais a menor custo. Mas com algumas dicas simples, toda oficina consegue melhorar consideravelmente a sua produtividade.
Você quer conhecer importantes dicas relacionadas ao processo de soldagem que são capazes de melhorar a produtividade? Então acompanhe as principais dicas neste conteúdo.
-
Conheça as características de cada processo de soldagem
Hoje em dia, a variedade relacionada ao processo de soldagem é bastante extensa, com processos TIG, MIG/MAG, eletrodo revestido entre outras. Porém, as características de cada um destes processos costumam variar, com cada uma garantindo maior produtividade para cada necessidade.
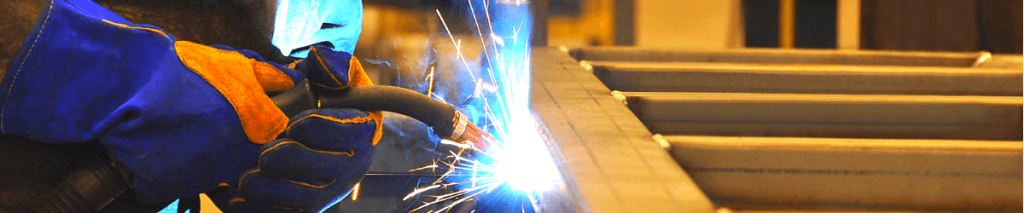
Dessa forma, para definir qual processo de soldagem você deve utilizar, é importante conhecer quais as características de cada um, para qual processo são recomendados, somente assim você irá encontrar vantagens e desvantagens entre eles, somente assim um elevado nível de produtividade será alcançado.
-
Saiba exatamente o que você quer cortar ou soldar
Conhecer as características do metal a ser soldado ou cortado é outro fator de suma importância para que se consiga ter elevada produtividade. Assim, é sempre importante que o processo de soldagem seja o mais apropriado para as características do metal.
As características mais importantes a serem consideradas para o metal são:
- Tipo de metal;
- Espessura deste metal;
- Condutividade térmica;
- Coeficiente de Expansão Térmica;
- Qualidade de corte desejada.
O correto entendimento sobre todas essas características do material irá garantir a escolha do melhor processo de soldagem, sendo esse o ponto de partida em busca da maior produtividade.
-
Evite o máximo de desperdício
Naturalmente, qualquer processo de soldagem envolve custos, dessa forma, para buscar maior produtividade é essencial que desperdícios sejam evitados, principalmente quanto ao uso de consumíveis, peças em não conformidade com o padrão exigido e trabalhos de reparação e consertos.
Assim, a primeira medida para reduzir os desperdícios do processo de soldagem é saber suas causas (como equipamento com problemas ou falta de manutenção, falta de treinamento e capacitação, falhas no projeto, entre outras).
Definido as razões do desperdício é hora de implementar ações corretivas que visam evitar casos de reincidência, elevando assim a produtividade. Tais ações podem ser desde treinamento do funcionário até reavaliação do projeto idealizado.
-
Priorize todas as manutenções e não deixe faltar materiais
Máquina de solda parada é um dos principais motivos para a redução da produtividade. Dessa forma, para que o processo de soldagem atinja o máximo de produção é essencial que as máquinas estejam em pleno funcionamento, com todas as manutenções em dia.
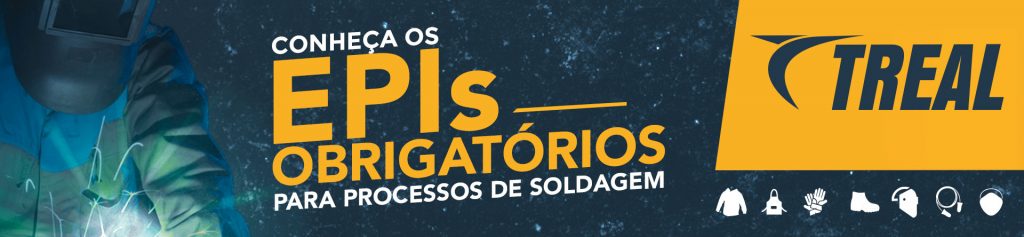
Além disso, alguns problemas mecânicos podem ser comuns nestas máquinas quando não há manutenção, caso das cremalheiras e pinhões, rolamentos de guia e lubrificação das guias.
Também é importante manter a área de trabalho sempre limpa, isso ajudará a máquina durar mais. Vale lembrar que partículas e fuligem que se acumulam nas máquinas não são apenas sujeira, elas são consideradas também como pó de metal que tende a contaminar as peças móveis, resultando em desgaste prematuro.
Além da manutenção, para manter a produtividade elevada é fundamental que nunca ocorra falta de materiais, principalmente os consumíveis e as peças sobressalentes da tocha utilizados no processo de soldagem, caso contrário o processo também irá ficar parado.
Para não faltar tais peças, manter um estoque suficiente para determinado período é sempre importante. Por isso, veja como está a sua média de uso de consumíveis, isso possibilita que você implemente um nível mínimo de estoque e quantidades de pedidos de rotina.
-
Melhore a qualidade do processo de soldagem
De fato, as dicas sugeridas até aqui são fundamentais para aumentar a produtividade, mas será o processo de soldagem propriamente dito que realmente definirá se houve ou não aumento da produtividade. Por isso, o momento da soldagem é o grande responsável pela maior produtividade.
Para conseguir isso é fundamental que o soldador considere corrigir alguns fatores durante o processo de soldagem, principalmente se ele acreditar que sua produtividade ainda não está no patamar desejado.
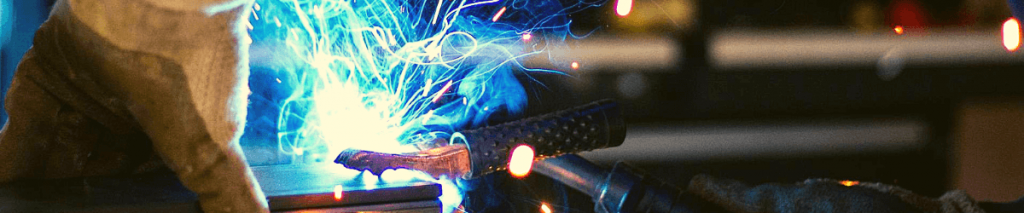
Entre as melhorias durante a soldagem, as mais comuns e recorrentes são:
- Consumo dos consumíveis: Inspecione e substitua os consumíveis se estiverem gastos. Também substitua sempre o bocal e o eletrodo ao mesmo tempo;
- Faça com que a distância entre a tocha e o trabalho esteja ajustada sempre na altura correta. Para isso, ajuste a distância da tocha à obra sempre para a configuração correta. Caso esteja usando o controle de tensão do arco, ajuste a tensão;
- Ajuste a velocidade de corte, conforme necessário. A velocidade de soldagem é um parâmetro que influência tanto no aspecto do cordão de solda quanto na determinação do aporte térmico trabalhado nas juntas soldadas, por isso verifique se a velocidade está correta;
- Identifique e conserte qualquer vazamento no sistema de fornecimento de gás, afinal, gás vazando significa dinheiro perdido, além de um grave risco à segurança. Além disso, gás contaminado pode ser um importante fator que afeta a qualidade da soldagem.
Por fim, é importante lembrar que todas essas melhorias só garantirão maior produtividade se ocorrer uma correta gestão de todos os setores, por isso adote uma posição firme introduzindo uma abordagem integrada, somente assim sua oficina atingirá valores mais elevados de produtividade.
Você quer saber mais sobre o processo de soldagem? Então conheça os riscos relacionados ao trabalho de soldador.
Comentários